
Avoiding this is the purpose of the derivative function. However, when there is a delay in response to the correction this leads to an overshoot and possibly oscillation about the set point. The longer the set point-to-actual value difference persists the greater the size of correction factor calculated. The integral function addresses this by considering the cumulative value of the error. The problem with this is that as the difference approaches zero, so too does the correction, with the result that the error never goes to zero. In proportional control the correction factor is determined by the size of the difference between set point and the measured value. However, fine control, and especially overshoot avoidance, requires the addition of derivative control. Many processes can be handled to an acceptable level with just the proportional-integral terms. Not every controller uses all three of these mathematical functions. PID stands for proportional-integral-derivative. The output is measured again and any required correction recalculated. If a difference is detected a correction is calculated and applied. The output of a device or process, such as a heater, is measured and compared with the target or set point. Even though many controllers provide auto tune capabilities, an understanding of PID tuning methods will help in achieving optimal performance.
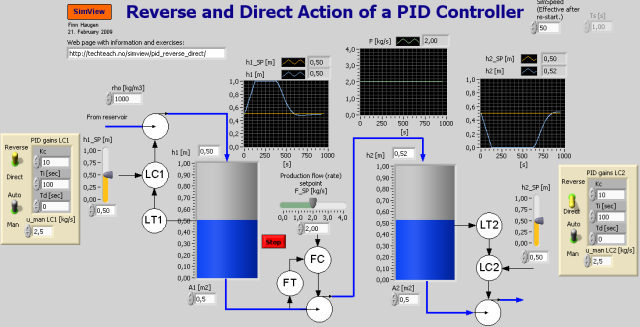
This White Paper from OMEGA Engineering discusses how to tune a PID controller. The process of finding these values is referred to as “tuning.” When a PID controller is tuned optimally, the device minimizes deviation from the set point, and responds to disturbances or set point changes quickly but with minimal overshoot. Although simple in concept, the mathematics underpinning PID control is complex and achieving optimal performance entails selecting process-specific values for a range of interacting parameters.
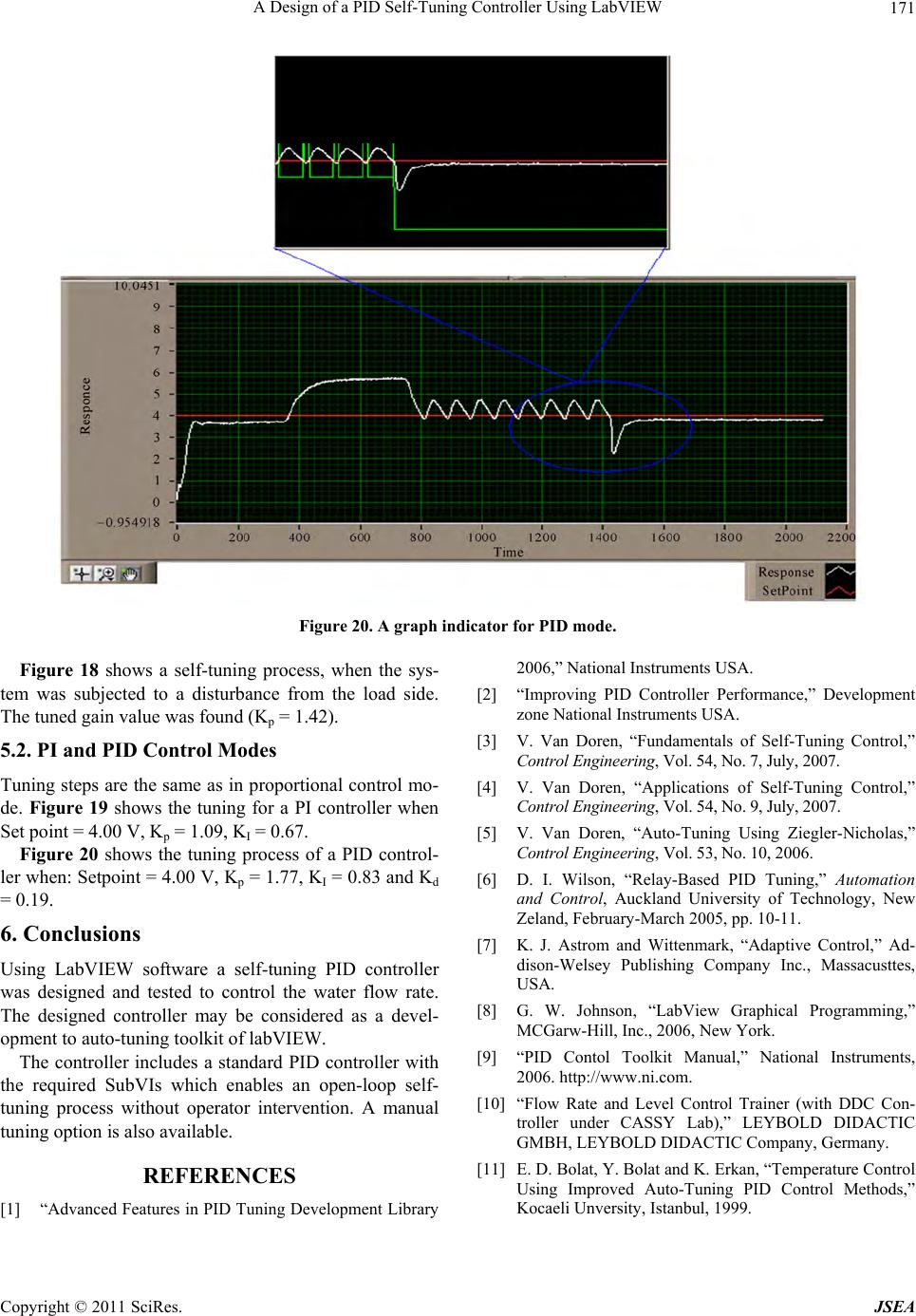
Any disturbance, such as when a product is added or withdrawn or a ramp function is applied, must be handled appropriately. To ensure consistent product quality the temperature inside an oven or furnace must be kept within narrow limits. Heat treatment processes exemplify the need for PID control.
